MRP (Material Requirements Planning)
Définition
MRP : Material Requirements Planning (Planification des Ressources de Production)
Le MRP est un outil clé qui permet de planifier, d’anticiper et de contrôler les différentes étapes de la production. Il intègre des données sur les besoins en matières premières, les capacités de production et les délais de livraison, facilitant ainsi une coordination optimale des opérations.
Imaginez un instant : vous êtes à la tête de l’approvisionnement d’usine de production, mais chaque matin, une question cruciale vous hante : avez-vous suffisamment de matières premières pour répondre à la demande du jour ? La réponse à cette question pourrait bien se trouver dans un système de gestion révolutionnaire : le MRP, ou Material Requirements Planning en anglais et plus couramment, Planification des Ressources de Production.
Comment fonctionne un MRP ?
Un MRP fonctionne grâce à un cycle en six étapes.
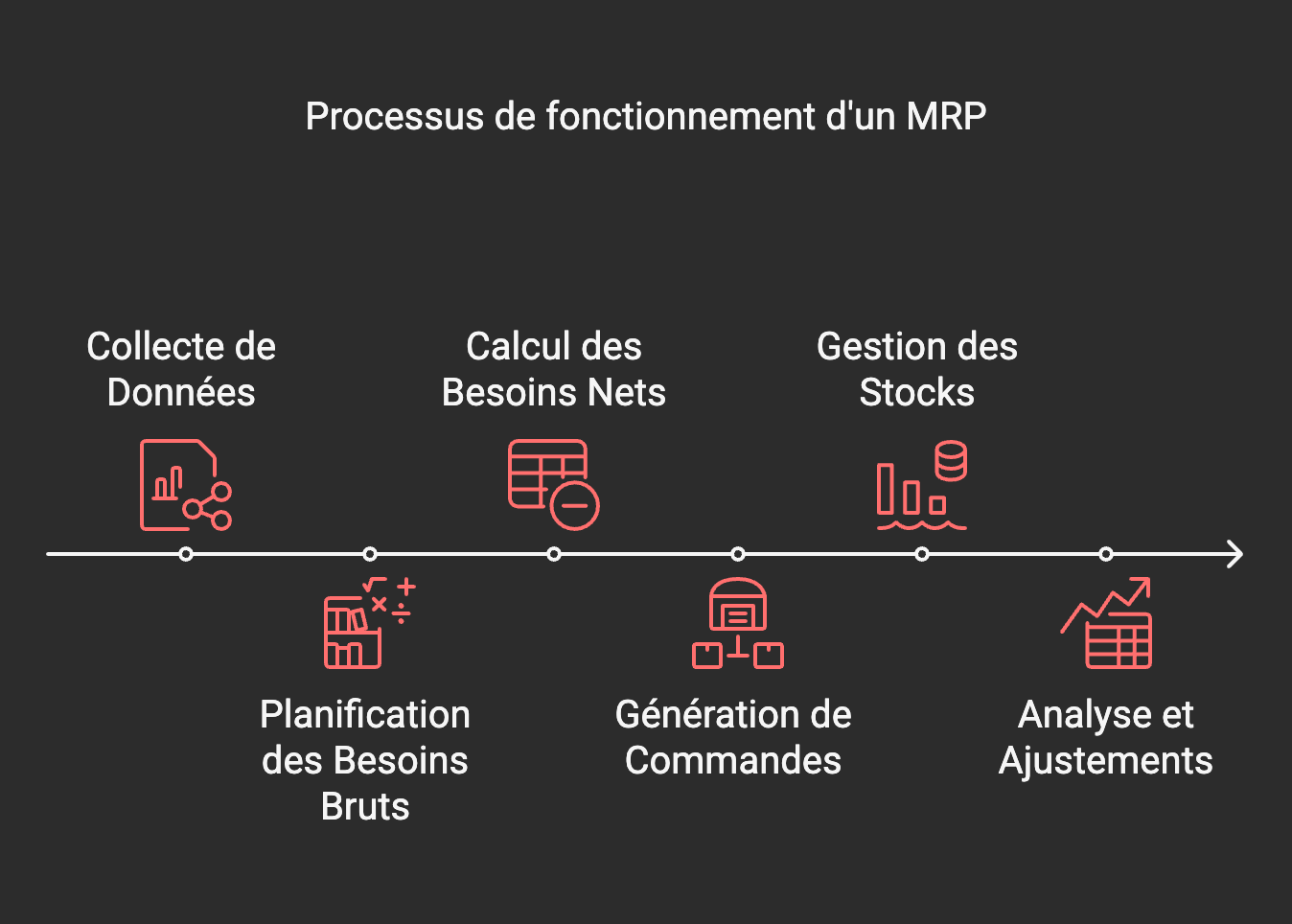
1. Collecte des données
Cette étape inclut la collecte des prévisions de demande basées sur des analyses des ventes passées, des tendances du marché et des campagnes marketing prévues.
Par exemple, une entreprise de fabrication d'équipements sportifs peut prévoir une augmentation de la demande pour des vélos en raison d'une campagne promotionnelle estivale.
En parallèle, les nomenclatures (BOM) des produits sont extraites, indiquant les composants nécessaires pour chaque modèle de vélo. Les niveaux de stock actuels et les délais d'approvisionnement des fournisseurs sont également analysés pour établir une base de référence.
2. Planification des besoins bruts
Une fois les données collectées, le MRP calcule les besoins bruts en matériaux.
Par exemple, si l’entreprise prévoit de fabriquer 500 vélos et que chaque vélo nécessite 10 pièces de cadre, le besoin brut en pièces de cadre sera de 5 000 unités. À ce stade, le logiciel prend également en compte les niveaux de stocks disponibles pour éviter les surachats.
3. Calcul des besoins nets
Après le calcul des besoins bruts, l'étape suivante est de déterminer les besoins nets. Cela se fait en sommaire les stocks disponibles. Si l'entreprise dispose déjà de 2 000 pièces de cadre, les besoins nets se réduisent à 3 000 unités (5 000 - 2 000).
Cette étape permet à l'entreprise de se concentrer uniquement sur ce qui doit être commandé ou produit.
4. Élaboration des ordres de fabrication et d'achat
Le MRP génère alors des ordres de fabrication et d'achat.
Pour les 3 000 pièces de cadre requises, le système pourra automatiquement recommander de lancer un ordre de fabrication pour la production en interne ou d'émettre un ordre d'achat auprès de fournisseurs pour s'approvisionner.
Ces recommandations sont définies par des délais de production pour garantir la disponibilité des composants au bon moment.
5. Gestion des stocks
Au fur et à mesure de la production et des achats, le MRP assure le suivi des niveaux de stock.
Retournons dans notre usine de vélos :
Chaque fois qu'une commande de cadre est produite, le MRP met à jour le stock en temps réel.
Si 1 000 pièces de cadre ont été fabriquées, les niveaux de stock sont ajustés automatiquement, permettant à l'entreprise de visualiser en direct ses ressources disponibles.
6. Analyse et ajustements
Enfin, le MRP fournit des analyses et des rapports réguliers.
Ces données permettent aux gestionnaires de comparer les prévisions de production avec la production réelle.
Si, par exemple, 450 vélos ont été produits au lieu des 500 prévus, il y a vraisemblablement un problème de production ou d'approvisionnement.
Basé sur ces résultats, l'entreprise peut ajuster sa production future ou ses stratégies d'approvisionnement pour mieux répondre à la demande.
Les trois composants clés d’un MRP
L’outil repose sur trois briques techniques :
- BOM (Bill of Materials) : Une liste détaillée des matériaux et composants nécessaires pour fabriquer un produit.
- Inventaire : Les niveaux de stock actuels des matériaux.
- Calendrier de Production : Les dates prévues pour la fabrication des produits finis.
Quelles différences entre un MRP et un ERP ?
Le MRP est un sous-ensemble essentiel des systèmes ERP industriels. Alors que le MRP se concentre sur la planification des besoins en matériaux et en capacités de production sur la base des prévisions de demande, l'ERP intègre de manière globale tous les processus d'une entreprise, y compris la finance, la gestion des stocks, la logistique et les ventes.
Par exemple, un système ERP peut suivre en temps réel les ventes et les niveaux de stock. Si une entreprise constate une augmentation des commandes d’un produit spécifique, le module MRP d’Odoo Fabrication, intégré à l’ERP, peut automatiquement recalculer les besoins en matières premières pour ajuster la production. Cela permet de minimiser les ruptures de stock tout en évitant des coûts excessifs liés à un surstock.
Les données maîtrisées par l'ERP fournissent des informations critiques pour optimiser la planification. Par exemple, si des retards de livraison de matières premières sont détectés, le MRP peut ajuster les calendriers de production en conséquence, permettant à l'entreprise de mieux gérer ses ressources et de répondre rapidement aux changements du marché.
Faut-il adopter un MRP ? Avantage et limites
Ce système présente plusieurs avantages, mais aussi quelques limitations qu'il convient de prendre en compte avant de se lancer dans son implémentation.
Avant tout, l'optimisation des stocks
n planifiant précisément les besoins en matériaux, le système réduit les excédents inutiles et évite les ruptures de stock coûteuses. Cette fonctionnalité permet non seulement de libérer du capital immobilisé dans des stocks excessifs, mais aussi d'améliorer le service client grâce à une disponibilité plus fiable des produits.
Des délais de production maîtrisés
Les délais de production deviennent plus prévisibles. Le système coordonne automatiquement les matériaux nécessaires avec les capacités de production, évitant ainsi les retards dus à des ruptures de composants ou à une mauvaise planification des ressources.
Après le délai de mise en place et les investissement initiaux, les gains de productivité deviennent généralement rapidement favorisable à la mise en place de ce système.
Une automatisation bienvenue
En supprimant une grande partie des tâches manuelles liées aux commandes et à la planification, vous pourrez réduire les erreurs humaines et se concentrer sur des activités plus stratégiques.
C’est un des jalons de l’industrie 4.0 qui permettra de décupler la productivité de votre entreprise via une transformation digitale.
Les défis à surmonter
Avant un déploiement, il faudra étudier le coût élevé d'implémentation et de maintenance. Mettre en œuvre un tel système nécessite souvent une réorganisation des processus internes et un investissement conséquent en temps et en ressources.
De plus, la complexité du système peut être un obstacle, nécessitant une formation approfondie du personnel pour s'assurer que l'outil est utilisé de manière optimale.
Le MRP dépend aussi fortement de la qualité des données fournies. Des données inexactes ou obsolètes peuvent fausser les prévisions et rendre le système inefficace.
Enfin, bien que puissant, un MRP peut manquer de flexibilité face à des changements soudains dans l'environnement commercial.
Une supervision humaine sera toujours nécessaire pour suivre ces épisodes exceptionnels.
C’est là qu’Odoo s’avère particulièrement robuste. Son approche no-code / low-code permet de l’adapter à des circonstances particulières pour ensuite reprendre des flux de production classiques.